Product application
Your are here: Home >> Product application >>The reaction kettle wall sticking reason and solution project
Hangzhou Huihe Equipment Co. Ltd:2013-11-25
Reaction vessel is belongs to a device of stainless steel container, sometimes reaction equipment and the phenomenon of glue to avoid is usually caused by two factors of reaction process and equipment itself. Specific please see below.
1. Reaction process factors
(1) Reaction temperature and time
When the reaction temperature below 80 celsius, if using ammonia chloride as catalyst, because the ammonia chloride reaction speed, PH shows don't come out, after being temperature, PH value drops rapidly, response speed up, wall sticking of polycondensation reaction, it can cause gel and appear, drop response speed.
In addition, the polycondensation reaction time is too long, resin molecular weight, high viscosity and easy appear wall sticking phenomenon. Therefore, operation should be the correct control of polycondensation reaction temperature and time, timely termination reaction. General reaction liquid temperature control within 95 celsius ~ is advisable.
(2) The reaction vessel wall temperature different.
Cooling medium temperature is too low or sudden cooling; make the reactor wall temperature and material temperature difference is too large, a contact tank wall sticking glue solution. So both heating and cooling should be performed within the reasonable temperature difference, usually steam temperature should be less than 180 celsius, the temperature difference between thermal shock should be less than 120 celsius, the cooling impact should be less than 90 celsius.
At the same time should be paid attention to determine the appropriate temperature at the inlet and outlet of the cooling medium, keep balance operation.
When the glue process indicators, such as temperature, pressure control unstable or excessive volatility, polycondensation reaction process resin unevenly, the wall is easy to sticking. So in production operations, it should slow pressure and temperature.
General ventilation with about 0.15 Mpa steam to keep after 2 ~ 3 min again slowly lift pressure rising. Speed per minute 0.1 ~ 0.15 Mpa is advisable.
(3) For high sulfate content in urea, when adding urea in the late resin polycondensation reaction, it is equivalent to join the curing agent, make resin is couplet net structure quickly, If handled not in time, it can make the resin curing in reaction kettle, Therefore, it should be chosen in the production of standard industrial raw material with urea, restrictions in the urea sulfate content below 0.01%.
2. Reaction equipment itself factors
(1) Flow characteristics
The flow of the material in the reaction vessel state will affect the degree of wall sticking; to improve the flow of the material can greatly reduce the degree of wall sticking effect. In the design of using the new turbine mixing way can make the material to produce radial flow, to improve the degree of adhering wall.
The reaction vessel wall sticking treatment methods
a. Vessel inner wall processing
The rough wall is hanging plastic easily. So we are in the process of machining the reaction vessel wall, heat exchanger and weld are fine polishing processing, it's to improve in the vessel is bright and clean degree, reduce wall sticking. In addition, through technology improvement, reduce reaction vessel in the solder joint, it also can hang in a certain extent, reduce glue phenomenon.
b. Eliminate the blind angle
It鈥檚 due to the unreasonable structure of reaction equipment and produce a corner where too much easy to stick wall. So we try to eliminate the equipment structure in the design on the corner. In the new type heat exchanger, heat exchange area is large; wall is good material flow is also reduced.
c. Feeding tube location
The reaction vessel feeding tube is a hard to stir dead angle, due to its local concentration of big nozzle, therefore, the wall is easy to cause stick, therefore it's shall reasonably determine the location of the feeding tube. We in the nozzle design using side next to the tube. At an angle of material fall slowly to the reaction liquid surface, to avoid glue liquid splash into the vessel wall, at the same time, uniform mixing, uniform distribution of material as far as possible, thus reducing the viscose.
In addition, the inner wall of the vessel viscose, high-pressure water spray cleaning device can be used to clean inside the wall.

Because the wood synthetic resin are used in industry has a certain viscosity, therefore, in the process of making glue wall sticking problems inevitably, if not timely technical processing, it will affect the heat transfer coefficient of the reaction kettle, increase the system of energy consumption.
In addition, due to the phenomenon of gel reaction kettle wall sticking phenomenon is mostly caused by technological reason, if you don't discovering and adjusting technology parameters in time, may directly affect the quality of adhesive solution. Using the above technical measures, it can minimize stick wall, glue production guarantee system run efficiently.
- The difference between steam heatin...
- Horizontal autoclave operation matt...
- What issue should be payed attentio...
- Daily use of fermentation tanks' fi...
- Simply discuss how fermentation tan...
- The difference between tilting jack...
- Parsing using and maintenance metho...
- Differences between Vertical Colloi...
- Working principle of colloid mill
- How much does it cost to order the...
- Application difference between coll...
- How to determine the time of using ...
- Sterilization pot
- Colloid mill
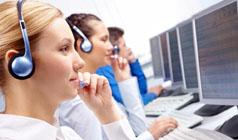
Add:33 Tangkang Road, Yuhang District, Hangzhou City, China
Tel : +86-571-86578098
Fax : +86-571-81604276
E-mail : manager@hhmachine.cn
QQ:2355663251 Phone/Wechat/Whatsapp:
+86 15268116877
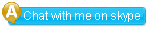
Skype: huihemachine
QQ:2355663252
MSN:huihemachine@outlook.com
